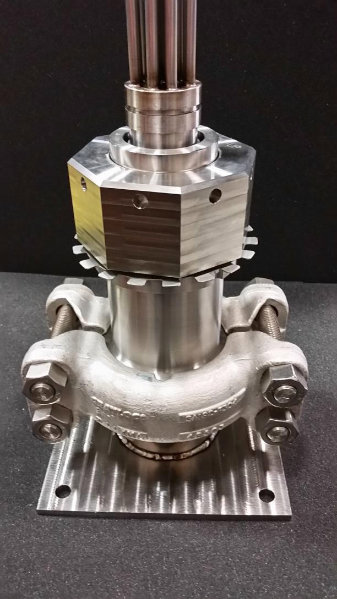
CETNA Mock Up
Background
The thermocouple nozzles on Westinghouse reactor vessel heads have two primary pressure boundary seals that have to be disassembled during each refueling outage: an upper and a lower Conoseal® joint. Each of these joints uses a Conoseal metal seal for the pressure boundary.
If a seal fails during a refueling outage, the system has to be depressurized and drained below the seal elevation. After replacing the seal, the system must be refilled and vented, adding more than a day to critical path work and resulting in a significant increase in man-rem exposure.
Additionally, wear and tear from routine maintenance may have degraded the original Conoseal flanges to the point where refurbishment is needed.
The Westinghouse Core Exit Thermocouple Nozzle Assembly (CETNA™) replaces the original Conoseal design on Westinghouse reactor vessels, eliminating leakage, and reducing personnel exposure and head area maintenance time.
Description
The CETNA replaces the upper Conoseal joint, leaving the head port adapter in place. A new seal housing that uses the existing clamp at the lower Conoseal joint is installed. This is a one-time operation performed as part of the CETNA installation.
The CETNA uses a graphite seal to replace the upper Conoseal, which provides the seal between the seal housing and the core exit thermocouple column.
After the new housing is installed and the reactor vessel head has been re-installed and tensioned, the balance of the CETNA parts are installed.
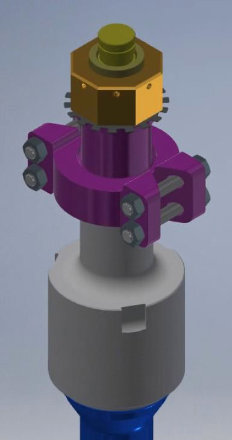
CAD Model of CETNA Installed
Three types of CETNA
- Flanged Version 3 (V3) Replaces the upper Conoseal joint on Westinghouse designed reactors, eliminating the need to disassemble the lower Conoseal joint during routine disassembly and reassembly.
- Canopy Seal Welded Replaces the upper Conoseal joint on Westinghouse designed reactors and eliminates the lower Conoseal joint with a new, longer head port adapter that's welded in place. This version of CETNA is best used when there's leakage in the lower Conoseal joint.
- Canopy less Only for new Westinghouse-designed replacement reactor vessel heads. This CETNA replaces the upper Conoseal joint, eliminating the lower Conoseal joint and the canopy seal weld entirely. This design is welded onto the head during head fabrication.
Benefits
- Cuts assembly time up to 75 percent and reduces radiation doses up to 85 percent
- Uses graphite seals that have been proven reliable in over 500 primary pressure applications for over 20 years
- Comes with a complete ASME Section III engineering documentation package
- Flanged V3 CETNA is simple to assemble and install:
- No field cutting or welding; mates to the existing instrument nozzle
- Reactor head can be removed without disconnecting the lower clamp
Experience
- CETNAs have been installed on over 60 reactors (over 220 CETNAs) in the U.S., Europe, and Asia since 1986 with an excellent performance record. The CETNA has been rigorously and successfully tested at typical plant design pressures and temperatures, as well as subjected to simulated seismic and loss-of-coolant accident events.
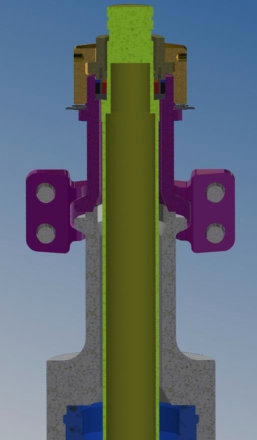
Section View of CETNA CAD Model