Background
PaR Nuclear, a subsidiary of Westinghouse Electric Company LLC, provides all types and sizes of cranes for use in nuclear power plants, with particular expertise and experience in outage-critical cranes. An outage-critical crane, a polar crane or reactor building crane, is one whose performance has the potential to impact refueling outage duration. As nuclear plants progressively reduce refueling outage durations, crane performance increasingly affects critical-path outage time.
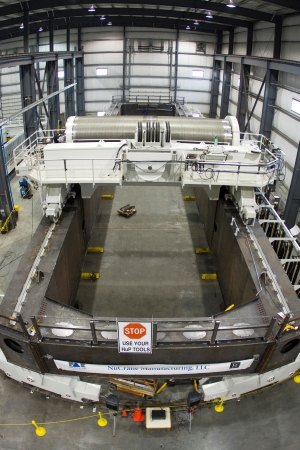
A 300-ton polar crane
Description
The PaR Nuclear hardware upgrade to PLC-based crane controls (featuring the Magnetek Variable Frequency Drive) meets the U.S. Nuclear Regulatory Commission’s NUREG-0554 and NUREG-0612, and ASME’s NOG-1 requirements. The upgrade applies to polar cranes, reactor building cranes and auxiliary building cranes. It features:
- "Safety Certified" PLC
- Remote Radio Controls
- Magnetek Drives
Major components available are:
- Bridge, trolley, main hoist and auxiliary hoist motors and drives
- Load cell and controller
- Radio remote control
Control enclosures and miscellaneous equipment include:
- Painted or stainless steel
- Nema-4 or 12
Mainline conductor system and wiring offer:
- Separate ground conductor
- Scoreboard display for load and system fault indication
Benefits
"Safety Certified" PLC:
- Provides digital communications between operator cab controls, crane operational inputs (e.g., limit switches, over-speed switches, brake-limit switches, drive-fault monitoring) and motor drives, simplifying the wiring to reduce installation time and quantity of failure modes
- Provides data to the scoreboard display, such as drive faults and hoist load
- Is capable of providing X-, Y-, Z-position indication and tracking, operational trending, safe load-path-zone development, troubleshooting diagnostics, redundant drive monitoring and operator touch-screen interface
Remote Radio Controls:
- Magnetek radio system remotely communicates operator commands directly to the drives
- Radio also has digital display of information for real time drive feedback and load indication
Magnetek Drives:
- Closed-loop vector control on hoists and open-loop vector control on traverse motions provide finite speed control
- Easy-to-use digital keypad and display of operating parameters and programming through multi-level password access.
- Load Check II™ continuously detects hoist overload conditions, halting upward motion and only allowing the load to be lowered; is able to provide an indication of load to a display
- Safe “Torque Off” provides a redundant hardware safety circuit that guarantees that motor and brake power are removed when an E-STOP switch or safety controller opens the drive input in a safety category three architecture, eliminating the need for external disconnects
- Adaptive Ultra-Lift™ allows for hoist operation up to two times base speed with a light loador empty hook, depending on mechanical limitations
- Brake torque proving after the drive sets and before releasing the brake(s)
- Programmable acceleration and deceleration ramps down to zero motor rpm, virtually eliminating hook swing and brake wear
- Greater than 100:1 speed resolution provides fine-positioning control, improving the efficiency of material-handling operations